Sustainable textiles
At Almedahls, we believe that sustainability should be woven into every thread of our work. From conscious material choices to responsibly crafted sustainable textiles, we prioritise manufacturing processes that benefit both people and the planet. Aiming for energy-efficient methods and reducing waste at every stage, we’re committed to creating sustainable fabrics that reflect our values and our vision to create A better place to be.
By choosing our products, you support a future where thoughtful design and environmental care go hand in hand. Our products for public and private spaces embody our commitment to textile sustainability, while our Five Zero Green programme, aligned with the UN’s Agenda 2030, ensures we deliver long-lasting, solutions for the next generation.
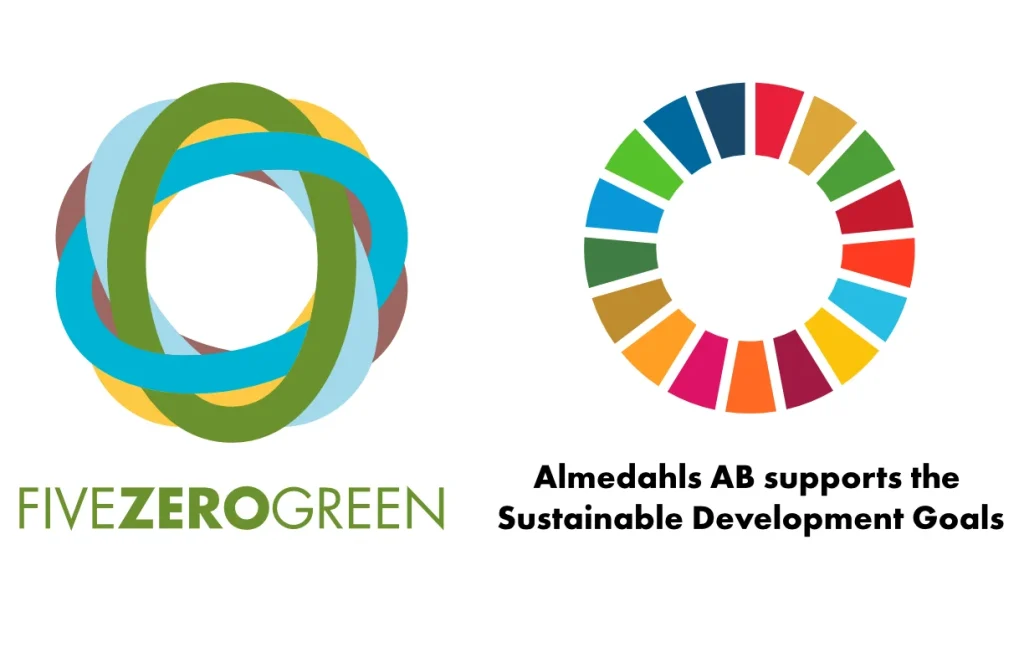
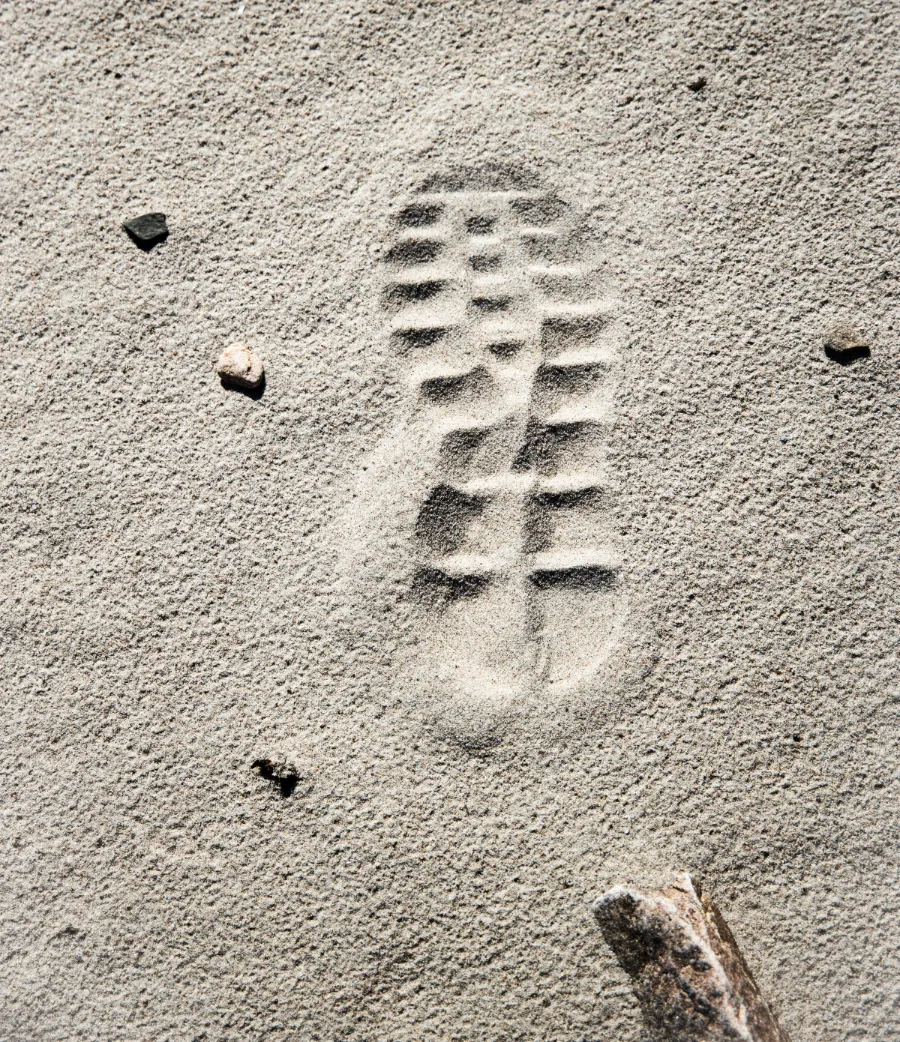
Sustainability - We have taken the environmental challenge further
For decades, we have pioneered textile sustainability, going beyond clean products to embrace clean production processes. Our focus isn’t just on creating high-quality sustainable textiles, but also on ensuring that our manufacturing methods minimise environmental impact and maximise positive outcomes.
Sustainability doesn’t stop with the product—it’s embedded in every decision we make. With our Five Zero Green programme, we have achieved CO2-neutral production today, well ahead of the European Commission’s 2040 targets. By choosing our fabrics, you’re supporting a brand that values innovation, respects the planet, and strives to leave a lasting positive legacy.
Our commitment to certified sustainability
We understand that certifications build trust. That’s why our fabrics carry the globally recognised OEKO-TEX® Standard 100 certification, ensuring they’re free from harmful substances and safe for daily use. These credentials reaffirm our dedication to crafting fabrics that combine safety, beauty, and responsibility.
We’re also proud of our rating from EcoVadis, which places us among the top 2% of companies in the textile industry. This recognition underscores our leadership in textile manufacturing, highlighting our commitment to ethical practices, environmental protection, and transparency across the value chain.
Find more info about EcoVadis here
By choosing Almedahls, you’re investing in a future where high-quality design and sustainability come together seamlessly.
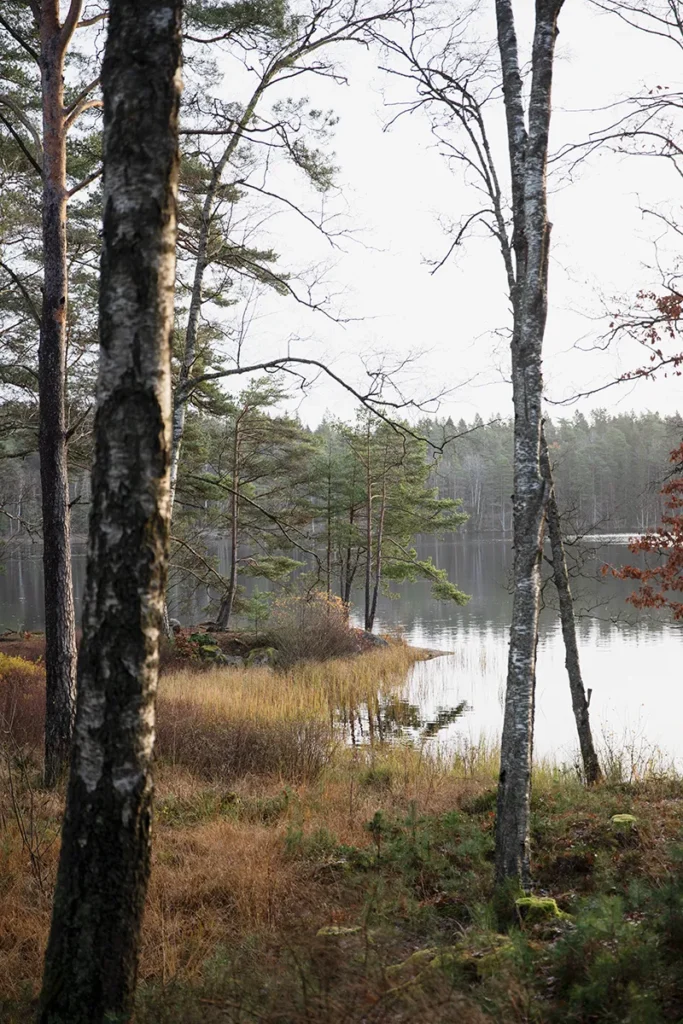
Do you want to know more about our sustainable textiles?
Contact usCertifications that set us apart
Lägg in CTA
accent heading
This is just placeholder text. Don’t be alarmed, this is just here to fill up space since your finalized copy isn’t ready yet. Once we have your content finalized, we’ll replace this placeholder text with your real content.
Our products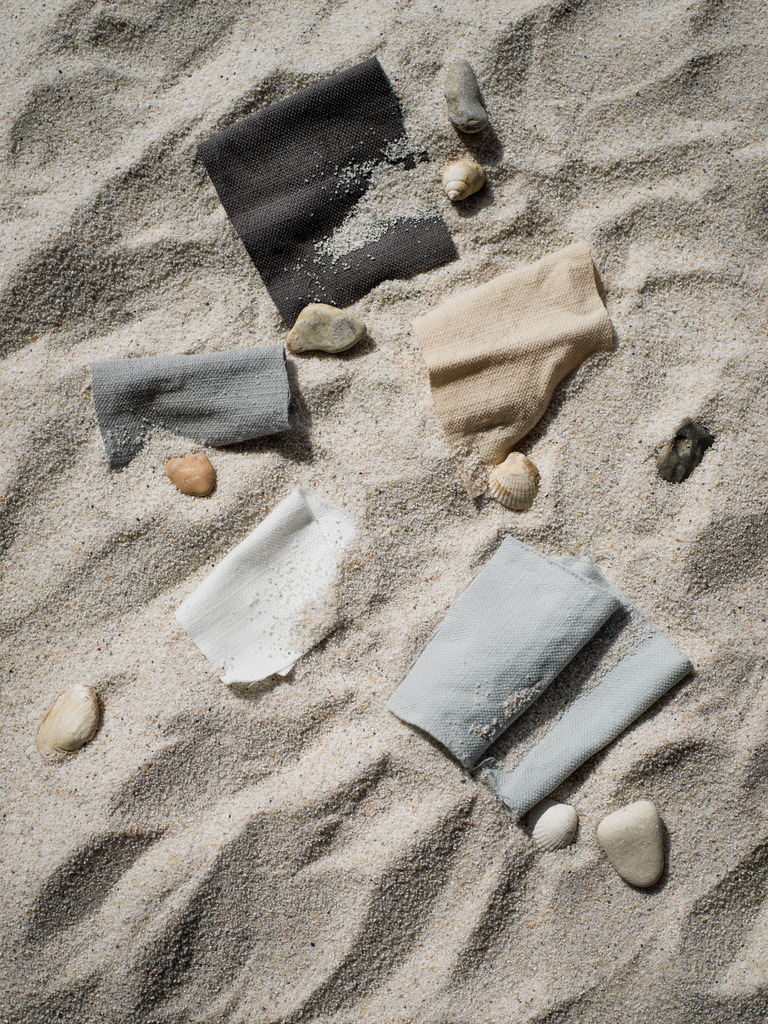